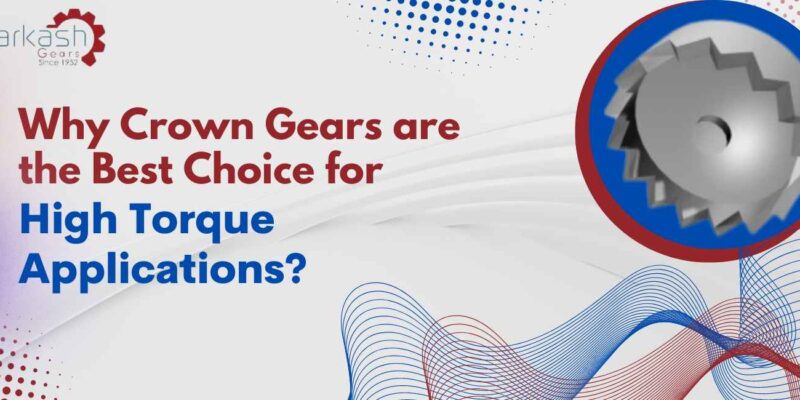
Why Crown Gears are the Best Choice for High Torque Applications?
When it comes to high torque applications, choosing the right gear can be a make-or-break decision. Enter crown gears – the unsung heroes of many industrial and automotive machines. Crown gears are known for their durability, precision, and strength in handling heavy loads with ease. In this blog post, we’ll dive into what makes crown gears so special and why they’re often the best choice for high torque applications. Whether you’re an engineer or just curious about how things work, keep reading to discover more about these impressive pieces of machinery!
What are crown gears?
Crown gears, also known as contrate gears or bevel gears, are a type of gear that is often used in high torque applications. Unlike other types of gears, such as spur and worm gears, crown gears have teeth that are cut at an angle to the face of the gear. This allows them to transmit power between two shafts that are oriented at different angles.
The shape of crown gears makes them ideal for use in machinery where space is limited or where it’s necessary to change the direction of rotation between two perpendicular shafts. They’re commonly found in automotive differentials and transmissions, industrial equipment like printing presses and lathes, and even in some musical instruments like pianos.
One important thing to note about crown gears is that they must always be paired with another bevel gear – they cannot mesh with any other type of gear. This means that when designing a machine or selecting replacement parts for one already in use, it’s crucial to ensure that both the pinion gear (the smaller of the two) and crown gear are compatible with each other.
While not as well-known as some other types of gearing systems, crown gears play an essential role in many machines we rely on every day.
How do crown gears work?
Crown gears are a type of bevel gear that operates on the principle of meshing two angled teeth. Unlike other bevel gears, crown gears have teeth that face perpendicular to the plane of rotation. This is what makes them unique and beneficial for high torque applications.
When two crown gears come together, their teeth interlock and transfer rotational force between each other. This design allows for smooth power transmission without any slippage or loss in efficiency.
The angle at which the teeth are cut also plays a crucial role in how crown gears work. The angle must be precisely calculated to ensure optimal contact between the gear’s surfaces, thus preventing any unnecessary wear or damage over time.
One advantage of using crown gears is their ability to handle large amounts of torque due to their unique tooth geometry and surface area contact. They’re also very durable and can operate in extreme temperature conditions without failure.
However, one disadvantage is that they can create more noise than other types of gears due to the increased surface area contact during operation. Additionally, because they require precise calculations when designing them, they tend to be more expensive than standard straight-cut spur or helical gears.
Understanding how crown gears work can help engineers make informed decisions about when and where to use them in high torque applications.
Advantages of using crown gears
Crown gears, manufactured by gear manufacturers in Ludhiana, offer several advantages that make them an excellent choice for high torque applications. One major benefit is their ability to handle large amounts of load without experiencing significant wear and tear. This makes crown gears ideal for heavy-duty applications such as mining machinery, construction equipment, and industrial gearboxes.
Another advantage of using crown gears is their efficiency in transmitting power. Crown gears provide a smooth transfer of energy between two shafts at right angles to each other with minimal power loss due to friction or slippage. This means less wasted energy and increased overall system performance.
Crown gears are also versatile in terms of configuration options, making them suitable for use in a wide range of systems requiring different ratios and speeds. They can be used alone or combined with other types of gearing systems such as spur or helical gears.
Furthermore, crown gears have relatively low noise levels compared to other types of gear designs resulting from the rolling contact between the teeth instead of sliding contact which reduces vibration and noise generated during operation.
The benefits offered by crown gears make them an attractive option for many high torque applications where reliability, efficiency, versatility are essential factors when designing a system operating under harsh conditions over long periods
Disadvantages of using crown gears
While crown gears are an excellent choice for high torque applications, there are also some disadvantages to consider.
One potential drawback of using crown gears is the increased noise and vibration they can produce compared to other gear types. This is due to the teeth of a crown gear being angled rather than straight, which can create more friction and therefore more noise during operation.
Another disadvantage is that crown gears require precise alignment in order to function properly. If not aligned correctly, they may wear unevenly or even fail completely. This means that careful installation and maintenance is required when working with these gears.
In addition, because of their complex design, crown gears can be more expensive to manufacture than simpler gear types such as spur or helical gears. This means that they may not be the most cost-effective option for every application.
Despite these drawbacks, however, there are many situations where crown gears remain the best choice for high torque applications. By understanding both the advantages and disadvantages of this type of gear, you’ll be able to make an informed decision about whether it’s right for your needs.
When to use crown gears
When it comes to choosing the right type of gears for high torque applications, crown gears can be a great option. But when exactly should you use them? Here are some situations where crown gears may be the best choice:
1. When you need high power transmission: Crown gears have a large contact area, which allows them to transmit more power compared to other types of gears.
2. When you need precise motion control: Crown gears offer smooth and continuous rotation, making them ideal for precision machinery applications such as robotics.
3. When space is limited: Because they mesh at 90 degrees, crown gears require less axial space compared to other types of gear sets like helical or spur gears.
4. When there are high loads involved: The shape of the teeth on a crown gear distributes load over a larger surface area than other types of gear sets, allowing them to handle higher loads without damaging teeth.
If your application requires high torque transmission and precise motion control in tight spaces with heavy loads involved then consider using crown gears from reputable manufacturers that specialize in producing this type of gear set for optimal performance and durability
Crown gear applications
Crown gears are commonly used in applications that require high torque and precision. One of the most common crown gear applications is in automotive differential systems, where they help to transfer power from the engine to the wheels. Crown gears can also be found in various industrial machines such as printing presses, textile machinery, and packaging equipment.
In addition to their use in traditional mechanical systems, crown gears have also found a place in robotics and automation. They are often used in robotic arms for precise movement control due to their ability to handle high loads while maintaining accuracy.
Crown gears have even made an appearance in entertainment technology, particularly within stage rigging systems. Their strength and durability make them ideal for handling heavy loads while ensuring smooth movement during performances.
Crown gears offer a versatile solution for many applications requiring high torque capabilities with precise motion control. As technology continues to advance and demand increases for more efficient and reliable machinery across industries, it’s likely we’ll see even more diverse uses of this essential component.
Conclusion
Crown gears are an excellent choice for high torque applications due to their unique design and advantages. They are highly durable, provide efficient power transmission, and can handle significant loads without experiencing wear or damage.
If you’re looking for a reliable and efficient solution for your high torque application needs, consider using crown gears from a reputable manufacturer. With the right gear design and material selection, you can achieve optimal results that meet your specific requirements.
Remember to weigh up the advantages against any potential drawbacks associated with using crown gears before making your final decision. Always consult with an expert in this area if you have any doubts or questions regarding which type of gear is best suited to your application.
By selecting a quality-built set of crown gears from a trusted manufacturer like Parkash Industrial Gears Inc., you’ll be able to enjoy long-lasting performance and excellent value for money over many years of use.
This Post Has 0 Comments