Our Services
Parkash industrial gears, is among one of the leading company in India with specialization in industrial gear manufacturing. Following the motto “Quality before Quantity”, at Parkash industrial Gears we believe in providing genuine quality products to our clients. We don’t make any kind of sacrifices on product quality. we have various types of imported machineries to produce world class and reliable products. we have machines from international brands like WMW Machinery Company, TOS, STANKO , GLEASON , DAEWOO PUMA, SYKES, DNW and many more.
Our main strength lies in the Satisfied Customer Return and aiming for International standard quality and in time delivery guaranteed through continual follow-up from inquiry untill delivery, for our Clients.Our services include manufacturing of:
With an far reaching experience of over 50 years, Parkash industrial Gears is an actively engaged in manufacturing, supplying and exporting gears to satisfy all kinds of industrial needs. Depending upon their usage in diverse applications.
Gears are made of various materials, if you are looking for a high performance gear with reliable operation, the selection of suitable material is very important. Based on applications, gears for high load capacity require a tough & robust material like carbon steel etc. Whereas, high precision gears require materials having lower strength and hardness rating.
Our Service & Product
We Manufacture
The Best Quality Gears For All Industry
We Manufacture Top-Notch Ground Gears For Customers By
Using Gear Grinding And An Advanced Inspection Facility.
Our Capablities
How we make the best gears and sprockets in the world.
Product Development
Warehouse :- Our plant include substantial warehouse space dedicated to storage of finished and semi finished goods available for immediate shipment or customization in our machine shop. Our inventory line includes thousands of line items, with hundreds of thousands of parts in stock in any time.
Sample identification :- We work with customers daily to identify sprockets and gears that are worn out, broken or of unknown specifications for some other reason. Our staff use their extensive knowlede of the geometry and manufacture of these parts, along with sophisticated measuring and calculation methods, to identify the specifications of items for re-manufacturing. This allows owners of such parts to obtain replacement parts where they might have had to replace entire gear boxes, mechanical systems or even machine tools.
Development & Management :- After order is placed with our company, it is reviewed and planned by a team of individuals . Work instructions and detailed CAD drawings are produced to aid manufacturingpersonnel in producing high quality products.
Fabrication
Overview :- Our staff of skilled operators employ sophisticated welding processes in the fabrication of gear, sprocket pulley and sheave blanks. Fabrication is carried out for product configurations ranging in size from 2” to 120” diameter. Using both common and unique processes a wide variety of configurations can be produced for original designs or as economical replacements for castings.
Welding :- From simple weld jobs to advance fabricated parts, Parkash Industrial Gears can provide you with a welded product that will fill your needs.
Machining
Turning
Our turning equipments is modern and our capabilities comprehensive across our product line. All turning requirements are handled in-house for maximum control of quality and delivery. Our CNC machine tools utilize state of art programming systems providing versatility , efficiency and accuracy .
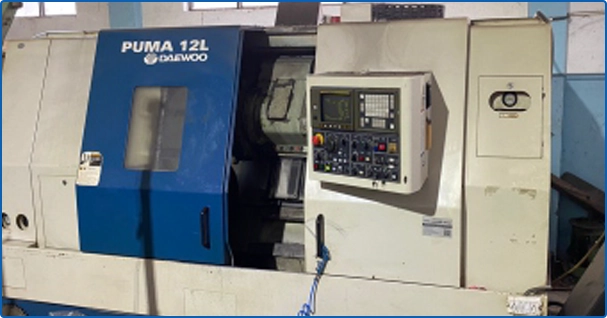
Miling & Driling
Substantial miling equipment is available here for meeting special machine needs of our customers. We have our shop set up for both quick turn around, short run jobs, as well as medium quantity production orders. Extensive drilling & tapping machinery is available as well for production runs of bolt hole circles for ready sprockets and common taper bushed shaft attachment systems.
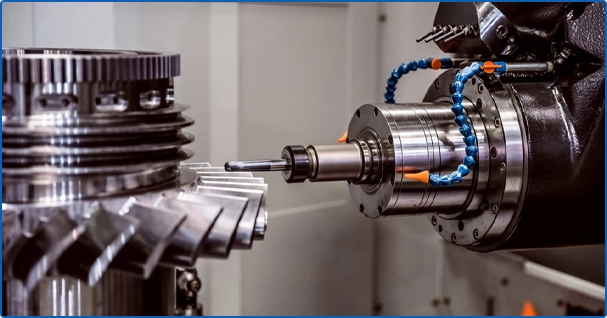
Grinding
In additions to our gear tooth grinding abilities we also have substantial experience and ability with grinding other surfaces such as precision ID/OD grinding on our Studer Grinder as well as surface grinding and honing . The Studer provides unparalleled accuracy on diameter, straightness, roundness, concentricity and surface finish.
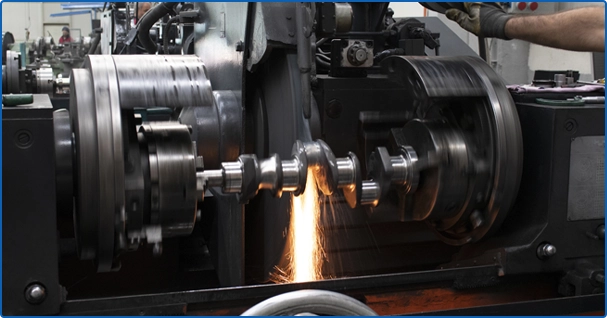
Gear Cutting
Our gear cutting capabilities are very diverse, including all of the most common gear types used in industry. Our inventory of gear cutting tools is extensive, covering a broad range of common and uncommon. Diametral (both Normal and Transverse), Circular, AGMA & Fellow Stub and Metric Pitches.
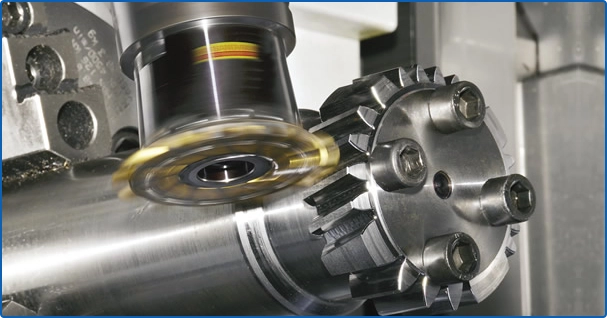
Sprocket Cutting
Today the company is among the most experienced and capable sprocket manufacturers in the world. Virtually every employee at Parkash Gear is involved with sprocket manufacturing, representing a vast level of experience in producing the best sprockets available. anywhere.
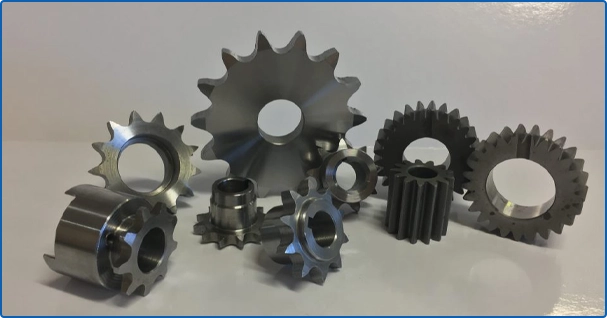
Heat Cutting
We have extensive induction heat treating equipment and experience and can provide excellent value by hardening the teeth of steel sprockets or gears. Other hardening services, such as carburizing can be provided through cooperation with outside sources.
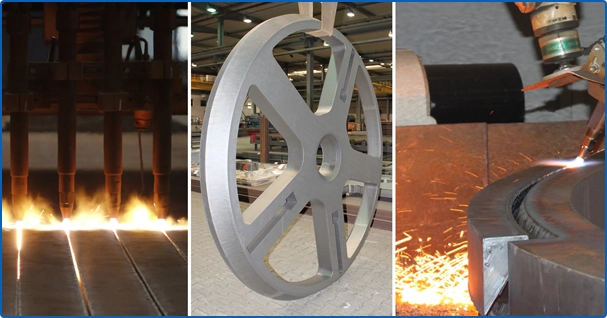
Reboring & Broaching
Final preparations of products for shaft mounting are made here. CNC and mechanical lathes provide straight and tapered OD and ID turning. Keyway and spline broaching, keymay miling and set screw drilling capabilities are extensive as well . Please inquire for specific requirements.
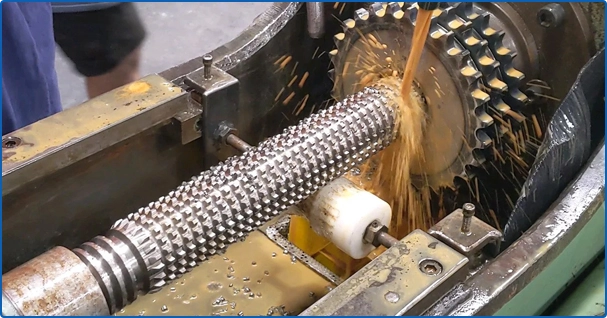
Infrastructure
We are having wide range of Gear Cutting Machines , CNC Turnings , Grinders , Broaching , Milling and Drilling.
Gear Cutting :-
1) Hobb Cutting , we are having all imported hobbing like TOS , Stanko , Pfauter , WMW, Sykes machines.
2) Sprial Bevel Gear cutting , we are having all Gleasons and WMW bevel generator.
Hobb Cutting
1) TOS Gear Hobbing (TOS fo10 , TOS fo16 , TOS fo25)
2) Stanko
3) Pfauter ( P630 , P900)
4) WMW Gear Hobbing
5) Sykes (Double Helical 3C)
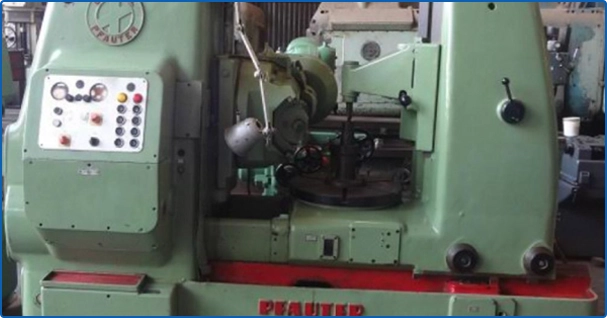
Gleason Machines and WMW Spiral Bevel Generator
a) Gleason No. 22 ( Rougher and finisher)
b) Gleason No. 16 ( 2 Rougher and finisher )
c) Gleason Lapper No. 119
d) Gleason Tester
e) Gleason Tool Sharpner No. 13 A
f) Gleason Tool blade setter
g) WMW 500 ZFTKK ( Bevel generator)
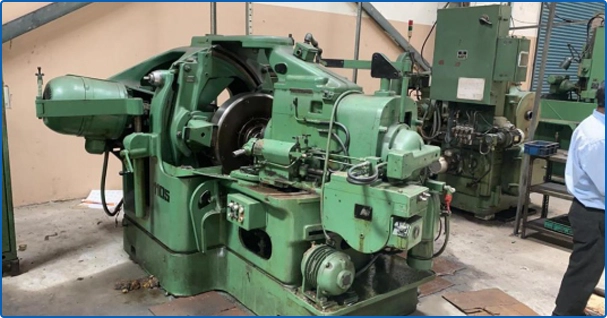
Gears Inspection
After teeth cutting of Spiral Bevel Gears Inspection is being done.
a) Roll on Tester
b) Run out
c) P.C.D check
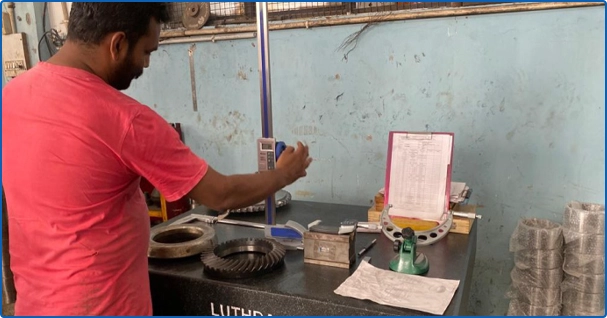
Turning
Our turning equipments is modern and our capabilities comprehensive across our product line. All turning requirements are handled in-house for maximum control of quality and delivery. Our CNC machine tools utilize state of art programming systems providing versatility , efficiency and accuracy.
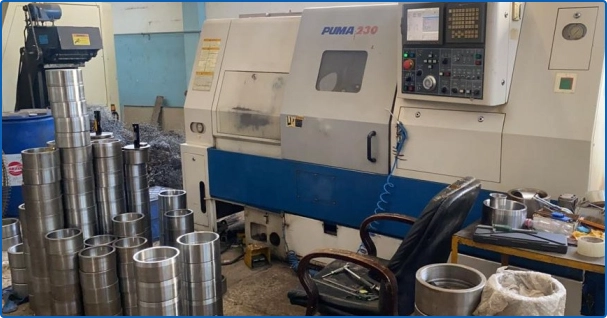
Turning Machines
We are having wide range of imported CNC Turning machines
a) DAEWOO 12L
b) PUMA 230
c) PUMA LYNX 200
d) JYOTI
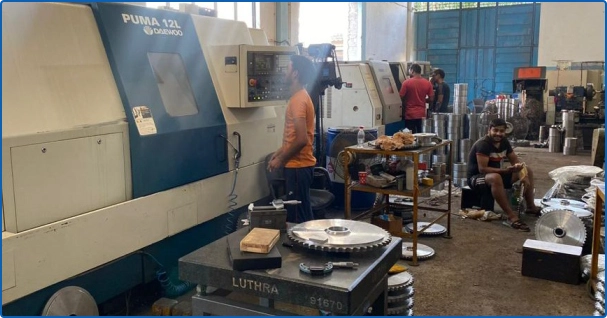
HEAT TREATMENT PROCESSES
PRE HARDENING :- Several heat treatments can be performed before or during the gear manufacturing process to prepare the part for manufacturing . In many cases these steps essential
1. Annealing :- Annealing is primarily indented to soften the part and to improve its machinability. There are several annealing processes , all of which involves heating to and holding at suitable temperature followed by cooling a specific rate usually through a critical range of temperatures.
2. Processes used for gears include :- Full or super critical annealing where a gear bland is heated 90-180 degree C(160-325 degree F) above the upper critical temperature (Ac3) of the steel and then slowly cooled in the furnance to around 315 degree C ( 600 degree F) Interstitial annealing where the gear is heated to a temperature between the upper and lower critical temperature ( Ac1) and then rapidly cooled and sub critically annealing, where gears heated C(50-100 degree F) below the lower critical temperature followed by a slow cool in furnance
3. Methods of Gears heat Treatment :- Basically the heat treatment of gears are given below :
Carburzing of Gears
Induction Hardening of Gears
Through- Hardening Gears
Quenching of Gears
Flame Hardening of Gears
Sealed Quenching
Deburring & Finishing
Removal of machining burrs and edges , marking of part numbers (both standard and customer specified) sandblasting , cleaning and coating of parts of rust inhibition and various other mid-process and final finishing operations are carried out in this development.
Inpection
Our products are inspected continuously throughout the manufacturing process by our machine operators. Experienced inspectors make a final inspection before products are shipped or put into inventory. Our final inspectors have a experience and a thorough knowledge of our products and manufacturing processes.