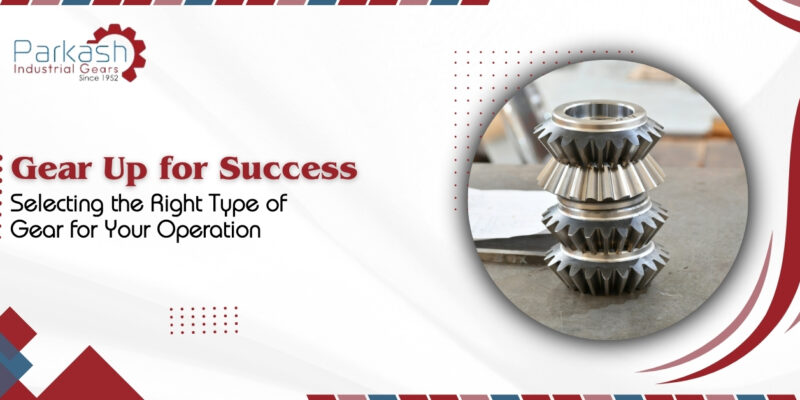
Gear Up for Success: Selecting the Right Type of Gear for Your Operation
Choosing the Right Type of Gear for Your Operation
In the realm of manufacturing and industrial operations, the role of gears is paramount. Gears are crucial in transmitting power and motion, enabling the smooth and efficient operation of various machinery and equipment. Whether in the automotive industry, aerospace sector, or any other field requiring mechanical power transmission, selecting the correct type of gear is essential for optimizing performance and ensuring operational success. As you embark on the journey of finding the perfect gear for your operation, understanding the intricacies of gear selection and collaborating with a reputable gear manufacturer are key steps toward achieving your objectives.
Understanding Gear Types and Applications
- Spur Gears – Spur gears are one of the most common types of gears, characterized by their straight teeth that are parallel to the gear axis. These gears are ideal for applications requiring high-speed rotation and uniform motion transmission, such as in automotive transmissions, industrial machinery, and power tools.
- Helical Gears – Helical gears feature teeth angled in a helix pattern around the gear axis, resulting in smoother and quieter operation than spur gears. They excel in applications requiring precise motion control and high torque transmission, such as in gearboxes, pumps, and heavy machinery.
- Bevel Gears – Bevel gears have cone-shaped teeth and transmit motion between intersecting shafts at right angles. They are commonly found in automotive differential mechanisms, marine propulsion systems, and agricultural machinery.
- Worm Gears – Worm gears have a screw-like gear (worm) that meshes with a toothed wheel (worm gear), enabling high gear reduction ratios and self-locking capabilities. They are commonly used in applications requiring precise speed control and torque multiplication, such as conveyor systems, lifting equipment, and machine tools.
Factors to Consider in Gear Selection
1. Load and Torque Requirements
One of the primary considerations in gear selection is the magnitude of the load and torque the gears will be subjected to. Understanding your application’s operating conditions and performance requirements is crucial for choosing gears that can withstand the required forces and deliver reliable performance over time.
2. Speed and Motion Requirements
Your application’s speed and motion characteristics will dictate the type of gear needed to achieve the desired performance. Whether you require high-speed rotation, precise motion control, or variable-speed transmission, selecting gears with appropriate tooth profiles, pitch angles, and gear ratios is essential for meeting your operational needs.
3. Space and Installation Constraints
Space limitations and installation considerations can also influence gear selection decisions. Depending on your machinery or equipment’s available space and mounting configuration, you may need to choose gears with specific dimensions, shaft orientations, or housing requirements to ensure proper fit and compatibility.
4. Environmental Conditions
The operating environment, including factors such as temperature, humidity, dust, and corrosion, can impact the durability and performance of gears. Selecting gears with suitable materials, surface treatments, and lubrication methods is essential for ensuring reliable operation and longevity, particularly in harsh or challenging environments.
Collaborating with a Reputable Gears Manufacturer
1. Expertise and Experience
Partnering with a reputable gear manufacturer brings valuable expertise and experience. Look for a manufacturer with a proven track record of delivering high-quality gear for diverse applications across various industries. Their knowledge of gear design, manufacturing processes, and material selection can help you make informed decisions and optimize performance.
2. Customization and Flexibility
Every application is unique, and off-the-shelf gears may not always meet your specific requirements. Choose a gear manufacturer that offers customization options and flexibility to tailor gears to your precise specifications. Whether you need custom tooth profiles, special materials, or unique geometries, a manufacturer with in-house design and engineering capabilities can accommodate your needs.
3. Quality Assurance and Reliability
Quality assurance is paramount regarding gears, as any defects or failures can significantly affect your operation. Select a gear manufacturer that adheres to stringent quality control standards and has robust testing procedures in place to ensure the reliability and performance of its products. Certifications such as ISO 9001 demonstrate a manufacturer’s commitment to quality and customer satisfaction.
4. Collaboration and Support
Effective communication and collaboration are essential for a successful partnership with a gear manufacturer. Choose a manufacturer that values open communication, actively listens to your needs and concerns, and provides responsive support throughout the design, manufacturing, and post-sales phases. A collaborative approach fosters trust and ensures that your gears are delivered on time and budget.
Conclusion
In conclusion, selecting the right type of gear for your operation is a critical decision that can significantly impact performance, reliability, and overall success. By understanding the different types of gears, considering key factors such as load requirements, speed characteristics, space constraints, and environmental conditions, and collaborating with a reputable gear manufacturer, you can ensure that your gears are perfectly suited to your application’s needs. Gear up for success by choosing the right gears for your operation and unlocking the full potential of your machinery and equipment.
This Post Has 0 Comments