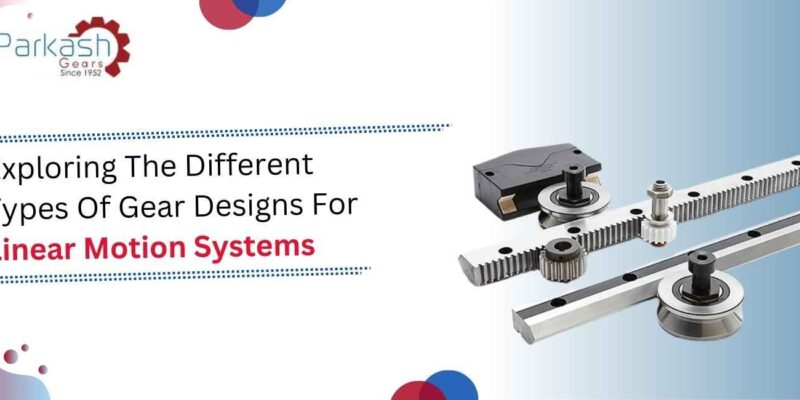
Exploring The Different Types Of Gear Designs For Linear Motion Systems
Do you want to learn more about the inner workings of linear motion systems? Do you want to learn more about the intriguing world of gear design? You’ve arrived at the correct location! In this blog post, we will look at the many types of gear designs for linear motion systems and discuss their advantages and disadvantages. Understanding these gear designs is critical when it comes to optimising your linear motion system, whether you’re a seasoned engineer or a casual hobbyist. So, fasten your seatbelts as we embark on an exciting journey through gears manufacturers in India!
What are Linear Motion Systems?
Linear motion systems are the backbone of many mechanical applications. Simply put, they enable objects to move in a straight line with precision and control. These systems are used in various industries such as manufacturing, robotics, automotive, and aerospace.
The key component of a linear motion system is the combination of rails or tracks and a carriage or slider that moves along them. This arrangement ensures smooth and accurate movement without any deviation from the desired path.
Ball screw-driven linear motion systems are a prominent type of linear motion system. It is made up of a threaded shaft (the screw) and a nut with ball bearings. These balls roll between the threads as the shaft spins, converting rotary action to linear motion.
Another commonly used design is belt-driven linear motion systems. They employ belts made of materials like rubber or polyurethane to transfer power from motors to carriages. The flexibility of belts allows for high speeds while maintaining accuracy.
Additionally, there are also rack-and-pinion driven systems where a gear (rack) meshes with another gear (pinion), resulting in precise linear displacement.
Whatever design you choose for your application, all linear motion systems strive for the same thing: smooth and reliable movement along an intended route. Choosing the correct type of linear motion system is critical for optimal performance, whether you’re developing automated machinery or designing cutting-edge robotics equipment!
The Different Types of Gear Designs for Linear Motion Systems
Gear designs play a crucial role in the functioning of linear motion systems. There are several types of gear designs that are commonly used, each with its own unique characteristics and advantages.
One popular type of gear design is the spur gear. Straight teeth that are perpendicular to the axis of rotation make up spur gears They are simple and efficient, making them suitable for many applications. However, spur gears can be noisy and may experience backlash.
The helical gear is another frequent gear design. Helical gears are distinguished by angled teeth that create a helix around the axis of rotation. When compared to spur gears, this design offers for smoother operation and a better weight-carrying capability. They do, however, generate axial thrust forces and can be more difficult to construct.
For applications requiring high torque transmission or compact size, worm gears are often used. Worm gears consist of a screw-like worm (the driving gear) meshing with a wheel (the driven gear). They provide high reduction ratios but tend to have lower efficiency due to increased friction.
In some cases, where precise positioning is essential, rack and pinion systems come into play. A rack is a flat-toothed bar while a pinion is essentially just another name for a small spur gear that meshes with this rack’s teeth directly converting rotational motion into linear motion or vice versa.
Each sort of gear design has its own set of advantages and disadvantages based on considerations such as load requirements, speed ratios, noise levels, efficiency requirements, and so on.
Understanding the many types of gear designs and their characteristics will enable you to select the best one for your unique linear motion system application.
Pros and Cons of Different Gear Designs
Gear designs play a crucial role in the performance and functionality of linear motion systems. Each gear design has its own set of advantages and disadvantages, which can greatly impact the overall efficiency and reliability of the system.
One common type of gear design is spur gears. These gears have straight teeth that mesh together to transmit power. They are simple to manufacture and cost-effective, making them widely used in various applications. However, they tend to generate noise and vibration during operation, which may not be ideal for certain sensitive environments.
Another popular gear design is helical gears. These gears have angled teeth that engage gradually, resulting in smoother operation with reduced noise and vibration compared to spur gears. They also offer higher load-carrying capacity and better efficiency due to increased contact area. However, their manufacturing process is more complex and expensive.
Bevel gears are another type of gear design commonly used in linear motion systems that require changes in direction or orientation. These gears have cone-shaped teeth that allow for efficient power transmission at different angles. They provide high torque transmission capability but may experience axial thrust forces during operation.
In contrast, worm gears offer high reduction ratios with compact size requirements, making them suitable for applications where space is limited. However, they tend to have lower efficiency compared to other gear designs due to greater frictional losses.
Each gear design has its own unique pros and cons that should be carefully considered when selecting the right one for your linear motion system application.
What type of Gear Design is best for your Linear Motion System?
When it comes to choosing the best gear design for your linear motion system, there are several factors you need to consider. Each gear design has its own unique characteristics and advantages, so it’s important to understand them before making a decision.
One popular type of gear design is the spur gear. This simple and cost-effective design consists of straight teeth on parallel shafts. Spur gears are known for their efficiency and ability to handle high loads, making them ideal for applications that require heavy-duty performance.
Another option is the helical gear design. Unlike spur gears, helical gears have angled teeth that gradually engage with each other. This results in smoother and quieter operations compared to spur gears. Helical gears also have higher load-carrying capacity and can transmit more torque, making them suitable for applications where precision and reliability are crucial.
For applications requiring precise positioning, worm gears may be the best choice. Worm gears consist of a threaded screw (the worm) paired with a toothed wheel (the worm wheel). This configuration allows for high reduction ratios while maintaining accurate positioning capabilities.
If space is limited or weight needs to be minimized, rack and pinion systems offer an excellent solution. Rack and pinion designs feature a flat rack that meshes with a pinion gear, providing linear motion instead of rotational movement.
The best gear design for your linear motion system will depend on your specific requirements such as load capacity, precision needs, noise levels, available space, and budget constraints. Consulting with experienced engineers or contacting reputable manufacturers can help you make an informed decision based on your unique application requirements.
How to choose the right gear design for your linear motion system
Choosing the right gear design for your linear motion system is crucial to ensure optimal performance and efficiency. With several options available, it’s important to consider a few key factors before making a decision.
You need to assess the load requirements of your system. Different gear designs have varying load capacities, so it’s important to choose one that can handle the specific weight and force exerted on your linear motion system.
Next, consider the speed at which your system needs to operate. Some gear designs are better suited for high-speed applications, while others excel at slower speeds with higher torque requirements. Understanding your desired speed range will help narrow down the suitable options.
Another factor to consider is a backlash or play within the gears. Certain gear designs minimize backlash, resulting in smoother and more precise movement. If precision is critical for your application, choosing a low-backlash gear design is advisable.
Additionally, take into account environmental factors such as temperature and lubrication requirements. Some gear designs may be more tolerant of extreme temperatures or require specific types of lubrication for optimal performance.
Budget constraints should also be considered when selecting a gear design. While some advanced gear systems may offer superior performance features, they might come at a higher cost compared to simpler designs that still meet your functional requirements.
By carefully evaluating these factors – load capacity, speed requirements, backlash tolerance, environmental considerations, and budget – you can make an informed decision about which gear design suits best for your linear motion system’s unique needs
Conclusion
In this article, we have explored the different types of gear designs for linear motion systems. We have seen that there are various options available when it comes to choosing the right gear design for your specific application.
Each type of gear design has its own set of pros and cons. Spur gears offer simplicity and efficiency but may produce noise. Helical gears provide smoother operation but can be more complex to manufacture. Rack and pinion systems offer high precision but may require more maintenance.
When selecting a gear design for your linear motion system, it is essential to consider factors such as load capacity, speed requirements, accuracy, space limitations, and cost constraints. It is also crucial to evaluate the specific needs and demands of your application.
To make an informed decision, consult with experienced engineers or professionals who specialize in linear motion systems. They can help you assess your requirements and recommend the most suitable gear design for optimal performance.
Remember that not all gear manufacturers in India will offer the same level of quality and expertise as Parkash Industrial Gears, A Leading Gears-Manufacturer in India offers. Take time to research reputable manufacturers who have a track record of delivering reliable products.
By carefully considering these factors and working with trusted manufacturers, you can ensure that your linear motion system operates efficiently and reliably throughout its lifespan.
So whether you need precise positioning in industrial automation or smooth movement in robotics applications, understanding the different types of gear designs available will empower you to choose wisely based on your unique needs.
This Post Has 0 Comments