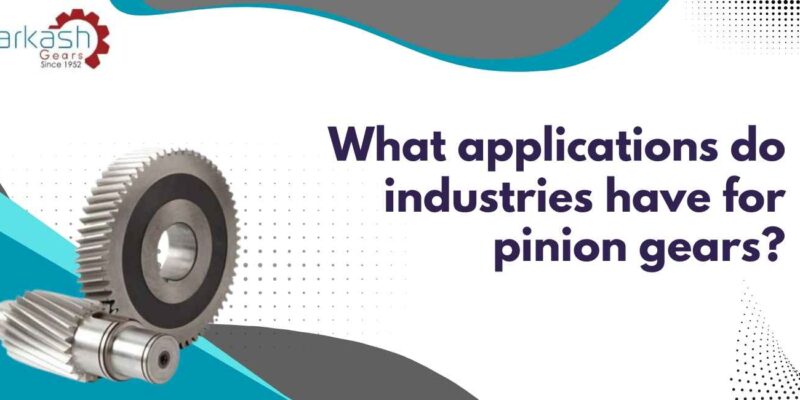
What applications do industries have for pinion gears?
Pinion gears may be small, but they play a vital role in many industries. From automobiles to heavy machinery, these little gears are instrumental in transmitting power and motion between rotating components. But what exactly are pinion gears? How are they made? And which industries rely on them? In this blog post, we’ll dive into the world of pinion gears and explore their applications across various fields. So buckle up and get ready for an exciting ride!
What Is Pinion Gear?
Gear manufacturers play a vital role in the production of various types of gears, including pinion gears. A pinion gear is a small cylindrical gear with teeth that mesh with the teeth of another larger gear, known as the rack. The pinion and rack combination is commonly used to convert rotational motion into linear motion or vice versa.
Pinion gears are typically made from materials such as steel, bronze, or aluminium. They come in various sizes and shapes depending on their intended use and can be customized to fit specific applications.
One of the key features of pinion gears is their ability to transmit torque efficiently between rotating components. This makes them a crucial component in many mechanical systems where power transmission needs to be precise and reliable.
Pinions can also be used in different configurations such as helical, spur or worm design depending on the specific application requirements. These designs can help improve efficiency by reducing noise levels and improving load capacity while maintaining high-speed performance.
Pinion gears may seem like simple components but they play an essential role across industries such as automotive manufacturing, heavy equipment production, and robotics technology among others.
How Are Pinion Gears Used?
Pinion gears are an essential component in various machinery and equipment. They are used to convert rotational motion into linear motion, making them ideal for applications that require power transmission at different angles.
One of the most common uses of pinion gears is in automotive vehicles, where they are used to transfer power from the engine to the wheels. These gears can be found in manual and automatic transmissions, as well as differential systems.
Another industry that utilizes pinion gears is the aerospace industry. In aircraft engines, these gears help adjust propeller pitch angle during flight. Pinion gears also play a crucial role in helicopter rotors by converting engine torque into blade rotation.
In addition to transportation industries, pinion gears are also widely used in manufacturing equipment such as conveyor systems and lathes. They facilitate smooth movement while transmitting power between machinery components.
Pinion gear applications vary across industries but remain vital for efficient mechanical operations. Their versatility makes them a valuable asset for any manufacturer or engineer looking for reliable power transmission solutions.
What industries use pinion gears?
Pinion gears are widely used across many industries due to their unique ability to transmit torque in a compact and efficient manner. One of the most common applications for pinion gears is in automotive systems, where they’re used in steering mechanisms, transmissions, and differentials.
In addition to automotive, pinion gears are also commonly found in heavy machinery such as construction equipment and mining machines. They provide reliable power transmission that can handle high loads and rugged environments.
Pinion gears are also utilized in the aerospace industry for aircraft engines’ accessory drives. Due to their compact size and lightweight design, they’re an ideal choice for transmitting power within tight spaces while maintaining precise control over engine functions.
Other notable industries that use pinion gears, such as robotics engineering, medical devices manufacturing, marine propulsion systems engineering, among others, can benefit from the use of crown gears. Crown gears, known for their superior performance in high torque applications, are the best choice for these industries. Regardless of the application or industry involved, pinion gear manufacturers continue to innovate new designs made from advanced materials that offer improved performance with enhanced reliability. With their ability to handle high torque requirements, crown gears are a preferred option for achieving optimal results in various industrial settings.
How are pinion gears made?
Pinion gears are made through a process called hobbing. This method involves using a specialized tool, called a hob, to cut teeth into the gear blank. The gear blank is then heated and hardened to improve its durability.
Hobbing begins by mounting the gear blank onto a machine that rotates it at high speed. The hob is then brought into contact with the gear blank and slowly moved across its surface, cutting teeth as it goes.
The shape of the hob determines the shape of the teeth on the pinion gear. The number of teeth can also be adjusted by changing either the size or pitch of the hob used.
Once all of the teeth have been cut into place, any burrs or rough edges are removed from both sides of each tooth with sandpaper or other abrasive tools. Heat treatment is applied to harden and strengthen the pinion gears for optimal performance in their intended applications.
Making pinion gears requires precision craftsmanship and specialized equipment to produce high-quality results that meet strict industry standards.
Conclusion
To sum it up, pinion gears are essential components in various industries for transmitting power and motion between rotating shafts. These small yet powerful gears often work in tandem with larger gears to produce efficient mechanical systems.
As we have seen, the manufacturing process of pinion gears involves precision engineering and the use of high-quality materials to ensure durability and reliability.
Whether it’s automotive, aerospace, or even robotics, there is no denying that the applications for pinion gears are vast and continue to drive innovation across many different industrial sectors.
If you’re looking for a reliable supplier of high-quality pinion gears manufacturers in India under strict quality control standards, look no further than reputable manufacturers who specialize in producing these precision-engineered components. With their expertise and advanced technologies at your disposal, you can be sure that your application will benefit from top-notch performance and long-lasting reliability.
This Post Has 0 Comments