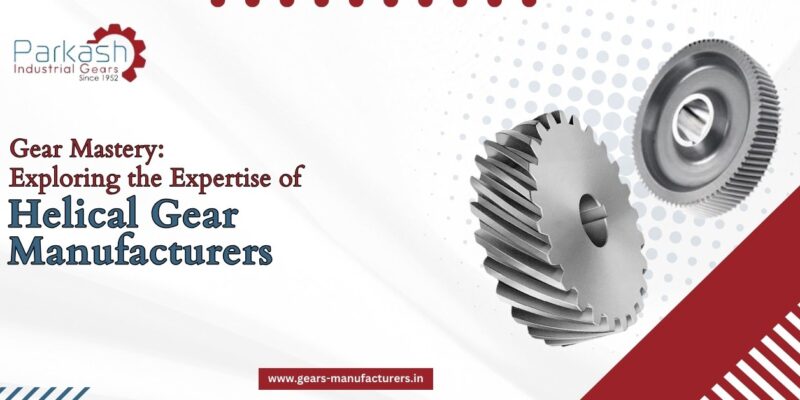
Gear Mastery: Exploring the Expertise of Helical Gear Manufacturers
Introduction
In the realm of mechanical engineering, helical gears play a pivotal role in transmitting power smoothly and efficiently. Helical gears, with their unique tooth orientation, offer superior performance and durability compared to other gear types. Behind the seamless operation of these gears lies the expertise of helical gear manufacturers. In this article, we delve into the world of helical gear manufacturing, exploring the mastery and precision that define these expert craftsmen.
Understanding Helical Gears
Before we dive into the expertise of helical gear manufacturers, let’s grasp the fundamentals of helical gear. Unlike spur gears, which have teeth parallel to the gear axis, helical gears feature teeth that are angled along the gear axis. This helical angle enables smooth and quiet operation, as the teeth engage gradually, reducing noise and vibration.
Key Characteristics of Helical Gears
- Helix Angle: The angle at which the teeth are inclined relative to the gear axis.
- Contact Ratio: The ratio of the tooth contact area during meshing, which affects load distribution and gear strength.
- Efficiency: Helical gears typically exhibit higher efficiency due to their tooth engagement characteristics.
Expertise in Helical Gear Manufacturers
Helical gear manufacturers play a pivotal role in ensuring the quality and precision of these essential components. From design to production, their expertise influences the performance and reliability of gears used in various industries, including automotive, aerospace, and industrial machinery.
1. Expertise in Gear Design
The journey begins with meticulous gear design, where manufacturers utilize advanced software and engineering principles to create optimal gear profiles. Helical gear manufacturers leverage their expertise to tailor designs based on specific application requirements, considering factors such as load capacity, speed, and noise levels.
2. Precision Manufacturing Processes
Crafting helical gears demands precision manufacturing processes that leave no room for error. Skilled technicians operate state-of-the-art machinery to cut, shape, and finish gears to exact specifications. From CNC machining to gear hobbing, each step is executed with precision to ensure dimensional accuracy and surface quality.
3. Quality Control Measures
Quality control is a cornerstone of helical gear manufacturing, where stringent measures are implemented to uphold the highest standards. Manufacturers employ advanced inspection techniques, including coordinate measuring machines (CMMs) and gear testers, to verify dimensional accuracy, tooth profile, and surface finish. Through meticulous quality control, manufacturers deliver gears that meet or exceed industry standards.
Advancements in Helical Gear Technology
As technology continues to evolve, so does the landscape of helical gear manufacturing. Manufacturers embrace innovation to enhance gear performance, durability, and efficiency.
1. Materials Innovation
The choice of materials significantly impacts gear performance and longevity. Helical gear manufacturers are at the forefront of materials innovation, experimenting with advanced alloys and surface treatments to improve wear resistance, reduce friction, and enhance overall performance.
2. Gear Coatings and Treatments
Surface treatments such as nitriding, carburizing, and coating technologies further enhance the durability and performance of helical gears. These treatments improve surface hardness, reduce friction, and minimize wear, prolonging gear life and minimizing maintenance requirements.
Future Outlook
The future of helical gear manufacturing is poised for continued innovation and advancement. With emerging technologies such as additive manufacturing (3D printing) and digital twin simulations, manufacturers can optimize design iterations, reduce lead times, and enhance overall efficiency. As industries demand higher performance and reliability from gear systems, helical gear manufacturers will continue to push the boundaries of innovation to meet evolving needs.
Conclusion
Helical gear manufacturers are the unsung heroes behind the seamless operation of machinery across various industries. Their expertise, precision, and dedication to quality ensure the reliability and performance of helical gears in critical applications. As technology advances and demands for efficiency grow, helical gear manufacturers remain at the forefront of innovation, driving progress and shaping the future of mechanical engineering.
This Post Has 0 Comments